Pentru ca 17″ si 17″ nu sunt identice
Pirelli Germania si-a optimizat procesul de productie cu ajutorul Autodesk Inventor.
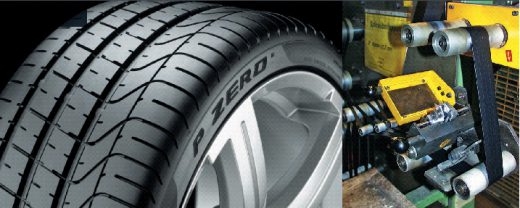
Peste 10 milioane de anvelope produse pe an pe linia de productie a Pirelli GmbH din Germania, in Hoechst/Odw. Aceasta cifra a putut fi realizata numai datorita productiei complet automatizate. In acest mod, toate procesele au functionat fara problem sub atenta supraveghere a departamentului de intretinere. Un instrument important aici il reprezinta solutia de proiectare 3D Autodesk Inventor.
„Multe masini de calitate superioara sunt echipate din fabrica cu anvelope Pirelli”, spune seful departamentului de proiectare, Dieter Lieb. „Suntem foarte mandri de buna cooperare cu producatorii de automobile de top din Germania.” Dar nu numai anvelopele de vara si de iarna pentru autoturisme sunt fabricate în Höchst. Aici se produc si anvelope off-road, iar productia de anvelope pentru motociclete devine din ce in ce mai importanta.
O suprafata de 367.225 m² este destinata anvelopelor de la prima pana la ultima componenta. Sunt si sectii de dezvoltare si “amestecare” a noilor compusi de cauciuc. Procesul de productie efectiv dureaza numai 72 de minute per anvelopa.
Produse din abundenta
Pirelli este unul dintre producatorii lideri la nivel mondial, dar totodata este si unul dintre furnizorii firmelor de productie de top. Masinile si echipamentele sunt furnizate la nivel mondial. „Munca noastra consta in stabilirea planului fiecarei fabrici si optimizarea acestuia pe baza modificarilor cerintelor proceselor automatizate de productie”, a declarat Dieter Lieb.
Acest lucru inseamna editarea si gestionarea planului de amplasare a cladirii fabricii, componentele tridimensionale ale masinilor, schemele electrice si alte date importante.
O provocare deosebita este marea varietate de produse. Marimea si latimea unei anvelope nu sunt, de departe, singurele caracteristicile care definesc, de exemplu, un carucior de transport pe care se deplasează materialul in pozitia de prelucrare.La prima vedere, doua anvelope de 17″ pot parea la fel, dar ele sunt diferite. Prin urmare, la Pirelli nu doar pneurile sunt diferite, ci si echipamentele de operare, proiectate si construite.
Actualizarea infrastructurii IT intr-un ritm de 3 ani
Pentru a ramane in pas cu dezvoltarile tehnologice, sistemele CAD existente sunt verificate la fiecare 36 de luni. Componentele cele mai des inlocuite sau actualizate pentru intrunirea cerintelor curente sunt computerele. De asemenea, Dieter Lieb si echipa sa verifica versiunile aplicatiilor software, pentru a depista inovatiile marcante din domeniu ce le-ar putea usura activitatea.
Ultima actualizare de la inceputul anului 2007 a reprezentat o schimbare completa. Astazi, sunt in operare zece statii de lucru CAD: sase posturi la sectiile mecanica si electrica Car (anvelope auto), doua posturi la Moto (anvelope de motocicleta) si doua posturi suplimentare pentru situatiile cu incarcare mare sau pentru uzul studentilor.
Angajatii sectiilor de productie si de mentenanta pot accesa direct prin intermediul unei baze de date interne datele din proiectare si listele de materiale.
O lume frumoasa si noua 3D
Pana la tranzitia din 2007, sistemul dezvoltat specific pentru sectiile mecanica si electrica a corespuns cu succes pe durata mai multor ani. Insa, cele mai importante doua motive pentru schimbarea lui au fost: in primul rand, furnizarea din ce in ce mai multor producatori de masini a documentatiei in format digital si, in al doilea rand, proiectarea 3D, atat de avansata acum, ale carei rezultate au dus la micsorari importante de costuri.
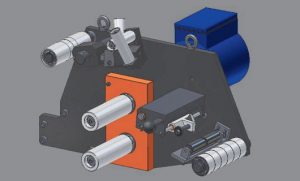
Deoarece majoritatea documentatiei digitale poate genera formatele DWG sau DXF, Pirelli avea nevoie de un sistem care sa poate gestiona aceste informatii. Pasul de la aceasta cerinta la Autodesk Inventor nu a fost mare; suita contine atat AutoCAD Mechanical pentru proiectarea 2D, cat si Autodesk Inventor pentru sistemele 3D. Proiectarea 2D este in continuare folosita pentru definirea amplsamentului fabricii, iar proiectarea echipamentelor este bazata pe partea de 3D.
In stanga: Pentru noile anvelope P Zero, o zona a linie de productie O-grade Nylon si un detaliu al echipamentului de taiere, in Autodesk Inventor.
Training de la zero
Angajatii de la Pirelli erau incepatori in proiectarea 3D CAD. Prin urmare, prin firma Haberzettl GmbH din Nuremberg, parte a grupului, s-a desfasurat primul curs de Inventor cu o durata de trei zile. Participanti au fost seful departamentului de proiectare si patru dintre angajatii sectiilor de proiectare si mentenanta.
In urmatoarele sase saptamani ulterioare cursului, proiectantii au utilizat cat mai des posibil noul sistem. Apoi a urmat inca o sesiune de doua zile pentru clarificarea intrebarilor si aprofundarea cunostintelor dobandite. „Bineinteles ca am utilizat intensiv linia de hotline a Haberzettl,” explica Dieter Lieb. „S-au obtinut multe cunostinte transmise colegilor nostri prin discutii si asistenta reciproca”.
Conversie necesara
In unele cazuri, vechiul sistem a ramas in continuare in uz, cu modificari minore sau ajustari aduse de proiectanti datelor existente. Preluarea integrala a planurilor existente in Autodesk Inventor se face extrem de rar. „Echipamentele si aparatele noastre sunt de regula dezvoltate pentru aplicatii specifice”, a declarat Dieter Lieb, „prin urmare sunt putine componente care vor fi reutilizate in proiectele urmatoare”. Daca totusi va aparea nevoia unui transfer, atunci acesta se va realiza foarte usor prin functiile de conversie ale Autodesk Inventor.
Euforie
Sase angajati din cele noua persoane instruite lucreaza acum exclusiv cu software-ul nou. Sunt aproape de „euforie”, spune Dieter Lieb. Ei au o usurinta de utilizare a instrumentelor datorita functionalitatilor integrate. Chiar si la doar trei luni de la introducere, sunt semne că se economiseste timp.
De asemenea, incantati sunt angajatii de la intretinere. Au in plus faţă de planurile standardizate de masini si componente chiar un model 3D, care este integrat in partea desene de executie. Chiar si cineva care este obisnuit sa citeasca planuri tehnice si desene şi de a le interpreta, gaseste reprezentarea 3D de ajutor si poate urmari mai usor echipamentul.
De la cordonul de sudura la piesa comandata
Timpul economisit de proiectanti cu generarea desenelor de executie este utilizat pentru aprofundarea aplicatiei software. La mare pret sunt functiile parametrice: „Se pot prelua cordoanele de sudura necesare „ca de pe raft”, se defineste distanta, iar aplicatia le plaseaza exact unde trebuie. Aceasta operatie este rapida si precisa”, spune Dieter Lieb. Biblioteca extinsa de piese standard este deja unul din punctele de atractie. Proiectantii nu mai trebuie sa caute in cataloage listate, pe Internet sau CD.
Urmatorul pas important a fost generarea automata a listei de materiale din modelul virtual 3D. Prin urmare, munca a fost accelerata in zona de proiectare. „O aplicatie software precum Autodesk Inventor este o aplicatie pe care trebuie sa ai sub control tot timpul, un proces similar cu optimizarea sistemelor noastre: trebuie sa fii mereu la curent cu ultimele dezvoltari,” a spus Dieter. „Dar cred că ne-am decis ca sistemul actual este fundamentul de cooperare pe termen lung – chiar dincolo de urmatoarele 36 de luni”.
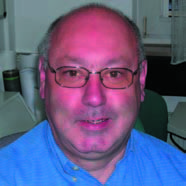
„Colegii mei sunt aproape “euforici”. Usurinta de utilizare a Autodesk Inventor este la fel de convingatoare ca functionalitatea sa consistenta. Chiar si la doar trei luni de la introducere arata ca se economiseste timp”, Dieter Lieb, sef departament proiectare.